Structural Extrusions
Replacing a fastener with an extrusion can be an easy win. Each fastener or weld point adds a step, while also adding a possible point of failure. E&E is an established leader in automotive structural extrusions in aluminum, steels, and alloys. We offer:
- Consistent on-time delivery—decades of performance awards from demanding manufacturers
- High part quality—known for best-in-class PPMs
- Overall reliability—we don’t just make a good part; we engineer a good solution that reduces costs
This is a family-owned metal stamping and extrusion operation. Even after half a century, we maintain an entrepreneurial attitude: nimble, flexible, responsive, and personal. Still, we deliver industry-leading quality, engineering, and manufacturing capabilities.
E&E is committed to a hands-on partnership. Your success is our business.
How do we consistently use steel, alloy, and aluminum extrusions to supply better solutions?
We Care.
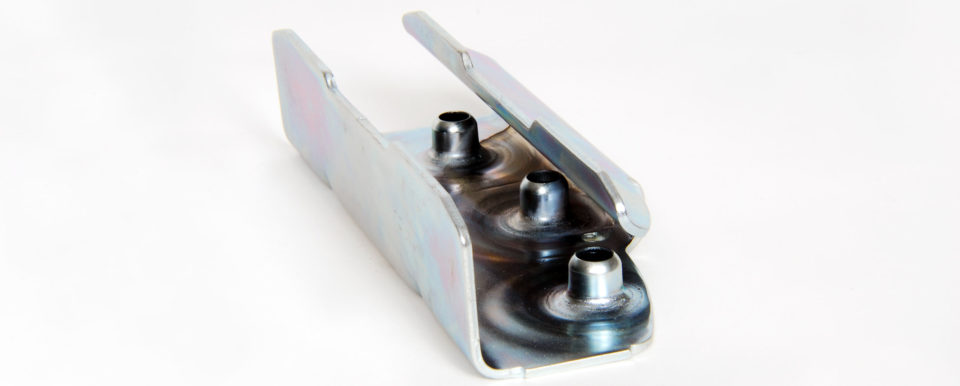
Custom Extrusions Reduce Costs
A vehicle component supplier approached E&E for help redesigning a problem part. The component in question consisted of a bracket and weld nuts. Their existing process resulted in customer rejection rates of 100 to 125 parts per million (PPM). Problems included missing nuts, upside-down nuts, off-location nuts, and holes blocked by weld slag. Making matters worse, these errors were often only discovered by the end customer late in their production process. The result: Ballooning costs, missed deadlines, enormous stress.
Even after spending over $100,000 on automated programmable sensors to support their quality assurance program, the automotive supplier could only reduce rejection rates to 50 to 75 PPM.
E&E reengineered the bracket. We eliminated weld nuts entirely, replacing these with threaded extrusions. This immediately saved them the cost of a new resistance welder ($125,000). It also eliminated a secondary operation and a QA step, reduced supply costs, freed up floor space, and removed any possibility of missing, misplaced, or obstructed weld nuts. The benefits of moving to a custom extrusion continued to accrue over the lifetime of that project.
Structural Extrusions
in Seating Components
Structural Extrusions
for Chassis Applications
Structural Extrusion Capabilities
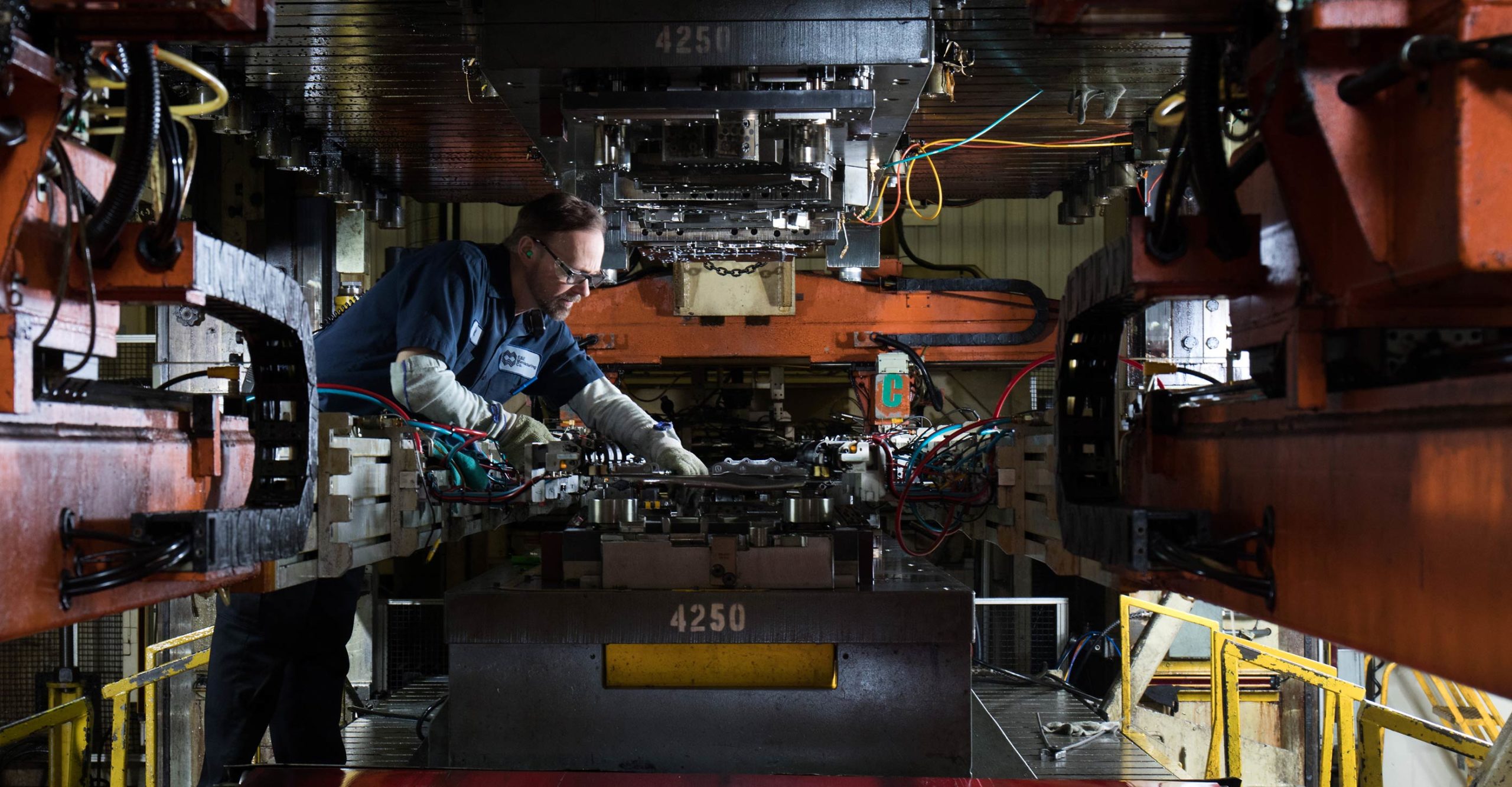
All extrusion shapes, profiles, and cross-sections:
- High volume, high quality, high value, low cost
- Extrusions from 0.5mm to 20mm thick (depending on part configuration)
- Extrusions within 25mm of each other (depending on part configuration)
- Hole size tolerances typically held to +/- 0.05
- Hole-to-hole location tolerance typically +/- 0.2mm or better
- Threaded or unthreaded (all tapping performed in-house)
All materials:
- Carbon steel
- Stainless steel
- High-strength and ultra high-strength steels
- Alloy steel
- Dual-phase materials
- Aluminum and other non-ferrous metals
Cost and weight reduction:
- Save weight and reduce cost through tailored material selection and custom
- Extrusion design
Value-added engineering:
- Need a performance specification? E&E has developed in-house performance specs for extruded fasteners
Advanced quality control:
- Fail-safe human/automated quality assurance
Structural Extrusion Products
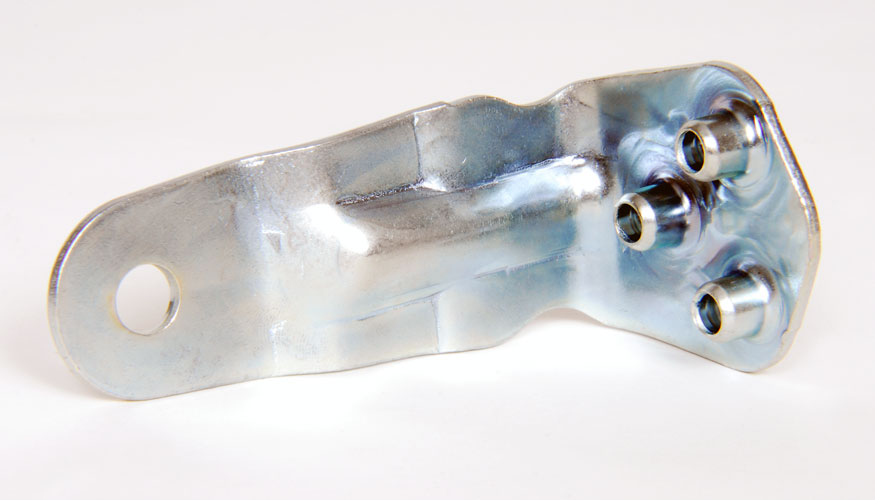
Product 1

Product 2
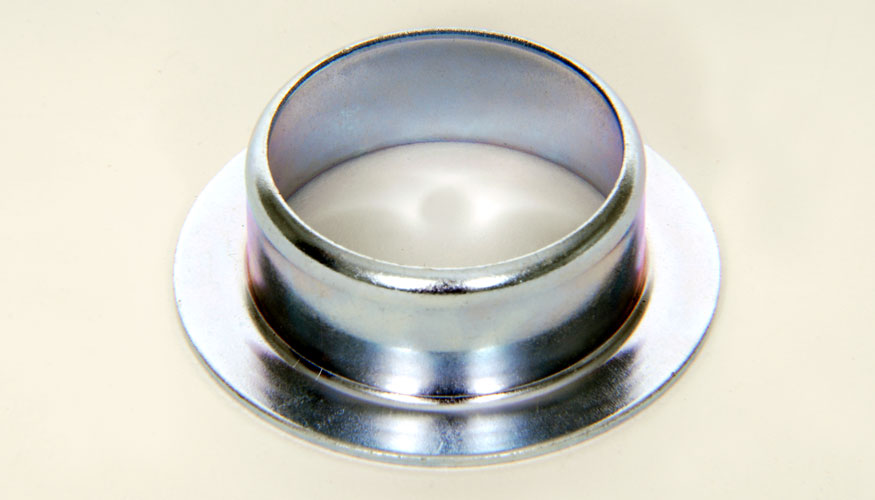
Product 3
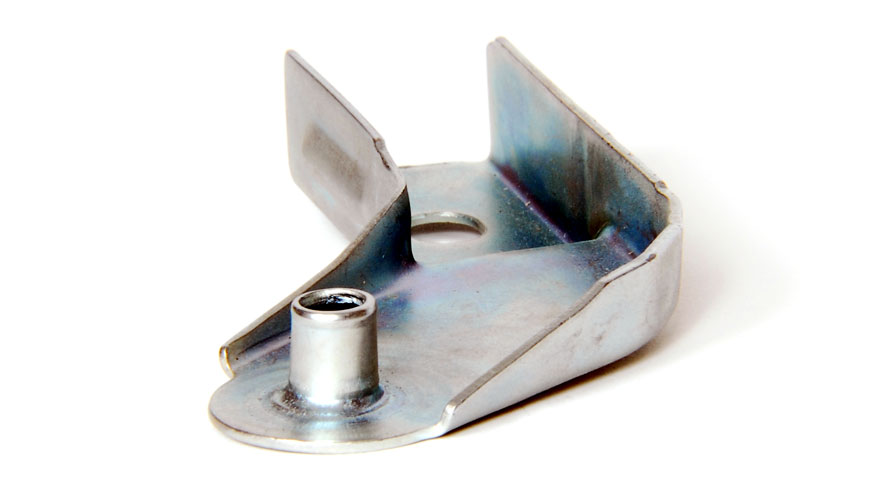